T: 905-664-8661
info@cuttingtoolpickers.com
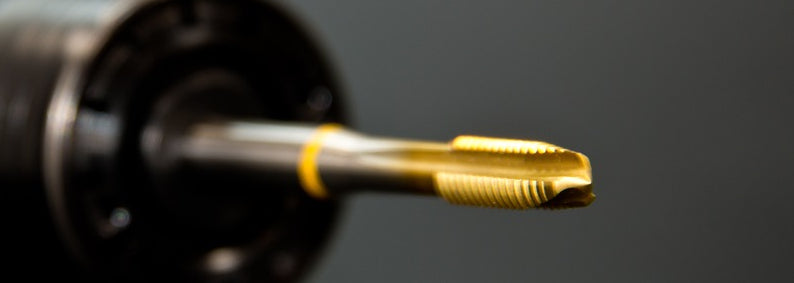
Basics of Tapping - Configurations & Uses
Machine taps and hand taps cut threaded holes called a “tap hole” or “pilot.” Taps are paired with a die, which is an external threaded part – like a nut to a bolt. With very sharp teeth that grip and cut into the pilot, taps scrape the inside wall creating a spiral thread as the tool is rotated in a clockwise motion; this is accomplished using either a tap wrench or machine. Rotating the tool counterclockwise will reverse it out of the pilot, or tap hole.
The configurations of taps are determined by the chamfer, which is at the tip of the thread length. The opposite end of the thread length is the shank. The tip of the shank is square in shape so that it fits securely into tool holders and wrenches. See diagram below:
MOST COMMON TAP CONFIGURATIONS
Taper Taps
With a 7-10 thread chamfer, this tool is able to gradually ease into material and is easier to align within a pilot, or tap hole. It is best used for first time thread cutting and through holes. Although, due to the chamfer, the first 7-10 threads aren’t clean and you can’t tap to the bottom of a blind hole.
Plug Taps
Plug taps have a 3-5 thread chamfer, which makes it harder to start a first thread. For this reason, plug taps are also known as “second taps.” If this tool is used for first time thread cutting, it is best to use a guided centre or fixture. Plug taps are best used for repairing existing threads or tapping deeper than the taper tap can do.
Bottoming Taps
These taps have the most shallow thread chamfer of only 1-2 threads. This design allows the tool to thread all the way to the bottom of its reach; hence the name. Due to the lack of chamfer, it can be difficult to control the alignment, so it is best to first thread with a taper or plug tap. A bottoming tap is best used to thread cut to the bottom of blind holes.
Spiral Flute
Like end mills, machine taps with spiral flutes create chip formation and chip evacuation. These taps are very easy to use and are a great tool for threading interrupted holes because it continues the threading past the open feature of an intersecting hole. Spiral flute machine taps are also great for threading blind holes.
Spiral Point
Spiral point machine taps have a spiral angle at the thread cutting tip with straight, shallow flutes. This design pushes chips ahead of the tool. Due to the shallow flutes and the spiral tip, there is access for lubricant to reach the cutting edges and makes the tap centrally stronger. This is a great tool for through holes and is most affordable for CNC power tapping.
*Blind Hole: a hole that does not break through the other side of a workpiece. "It is not possible to see through a blind hole."
*Through Hole: a hole made to go completely through the workpiece.
Comments
Leave a comment