T: 905-664-8661
info@cuttingtoolpickers.com
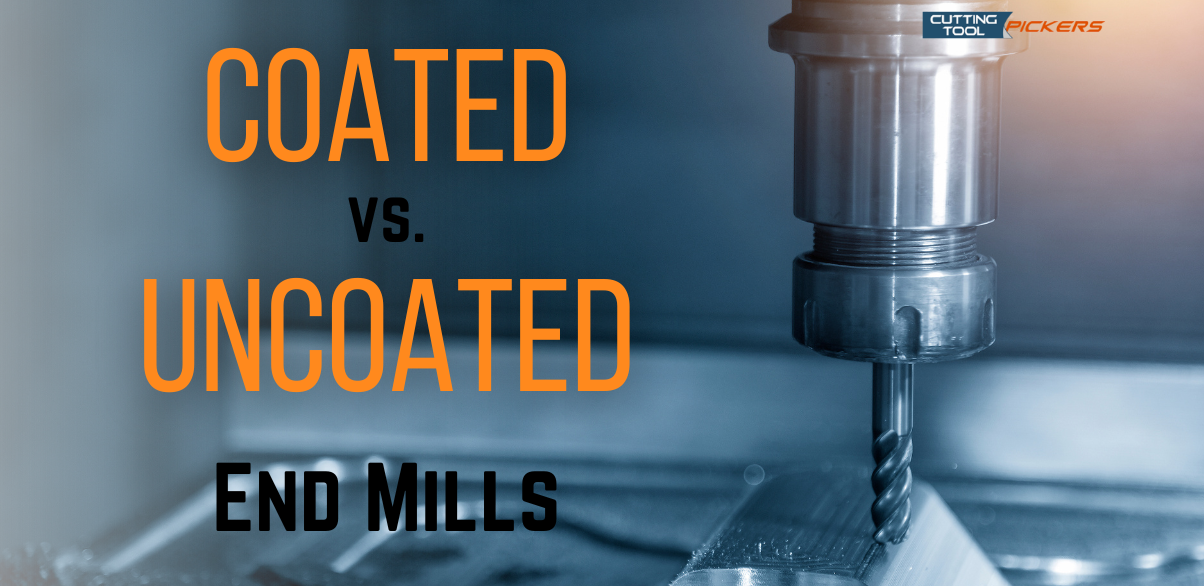
Coated vs. Uncoated End Mills
CNC machining is a highly precise process that relies on the right tools to deliver top-notch results. One key decision machinists face is whether to use uncoated or coated end mills. Understanding the differences and benefits of these options is vital for achieving success in CNC machining.
Uncoated End Mills:
-
Versatility: Uncoated end mills are incredibly versatile. They are suitable for a wide range of materials, from soft metals like aluminum to harder ones like stainless steel. This makes them a reliable choice for general-purpose machining.
-
Heat Dissipation: Uncoated end mills are excellent at dissipating heat during cutting. This feature is especially beneficial when working with materials that tend to generate excessive heat, as it helps prevent tool overheating and prolongs tool life.
-
Cost-Effective: Uncoated end mills are generally more budget-friendly than their coated counterparts. They offer a cost-effective solution for many machining applications, making them a preferred choice for those who are mindful of their budget.
Coated End Mills:
-
Enhanced Wear Resistance: Coated end mills are prized for their enhanced wear resistance. The coating, typically made of materials like TiN (Titanium Nitride) or TiAlN (Titanium Aluminum Nitride), provides a protective layer that significantly reduces tool wear and extends the tool's lifespan.
-
Improved Lubricity: The coatings on these end mills offer improved lubricity, which reduces friction between the tool and the workpiece. This results in smoother cutting and better surface finishes, particularly in challenging materials like hardened steel.
-
Higher Cutting Speeds: Coated end mills are better suited for high-speed machining due to their wear-resistant coatings. They can withstand increased cutting speeds and feed rates, leading to reduced cycle times and enhanced productivity.
-
Material Compatibility: Coated end mills are especially effective when working with abrasive or heat-resistant materials such as titanium, Inconel, and high-temperature alloys.
In conclusion, the choice between uncoated and coated end mills depends on your specific machining requirements. If you need versatility and cost-effectiveness, uncoated end mills may be the way to go. However, if precision, durability, and high-speed machining are crucial to your operation, coated end mills offer a significant advantage. Many machinists maintain a balance by using uncoated tools for standard tasks and reserving coated end mills for more demanding applications. Understanding the distinctions and benefits of these end mills is the key to making informed decisions and achieving optimal results in CNC machining.
Leave a comment